Innovations in Plastic Injection Mould Toolmaking
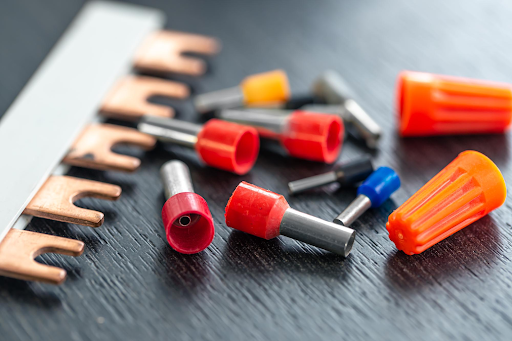
Plastic injection mould toolmaking stands as the cornerstone of modern manufacturing, wielding a profound influence on the quality, efficiency, and viability of production processes. In this discourse, we delve into the realm of toolmaking innovations, exploring recent advancements that are reshaping the landscape of the plastic injection moulding industry.
Advancements in Tooling Materials:
The advent of cutting-edge materials heralds a new era of durability and performance in injection mould toolmaking. Advanced steels and alloys, engineered to withstand the rigours of high-pressure injection moulding, offer enhanced durability and longevity, thereby reducing maintenance intervals and minimising downtime. These materials empower manufacturers to achieve unparallelled levels of precision and repeatability, laying the foundation for cost-effective and sustainable production processes.
Precision Machining Technologies:
In tandem with advancements in material science, precision machining technologies have undergone a renaissance, enabling the fabrication of intricate and complex moulds with unprecedented accuracy and efficiency. CNC machining, with its unparallelled precision and versatility, has emerged as the linchpin of modern toolmaking operations, allowing manufacturers to realise intricate geometries and fine-tune critical dimensions with unparallelled fidelity. Additionally, Electrical Discharge Machining (EDM) techniques offer a non-traditional approach to mould fabrication, leveraging electrical discharges to sculpt intricate features and contours with micron-level precision.
Additive Manufacturing in Toolmaking:
The proliferation of additive manufacturing, or 3D printing, has revolutionised the landscape of toolmaking, offering a panacea of benefits ranging from rapid prototyping to design flexibility and cost-effectiveness. By harnessing the power of layer-by-layer deposition, manufacturers can expedite the development cycle, iterate on designs with unprecedented agility, and realise complex geometries that were hitherto deemed unattainable. Moreover, additive manufacturing enables the consolidation of multiple components into a single, integrated unit, reducing assembly complexity and minimising material waste.
Automation and Robotics Integration:
Automation and robotics are emerging as linchpins in the realm of toolmaking, imbuing manufacturing processes with unprecedented levels of efficiency, precision, and scalability. From automated material handling systems to robotic machining centres, the integration of automation technologies streamlines production workflows, reduces labour costs, and enhances process repeatability. Furthermore, robotic systems offer unparallelled levels of dexterity and agility, enabling manufacturers to tackle complex machining tasks with ease and precision.
Case Study:
Consider the case of a leading injection moulding manufacturer tasked with producing intricate automotive components with stringent dimensional tolerances. By leveraging advanced materials such as high-strength tool steels and implementing state-of-the-art CNC machining techniques, the manufacturer achieved a 40% reduction in production lead times while simultaneously enhancing part quality and consistency. Furthermore, the integration of robotic automation systems enabled the manufacturer to streamline production workflows, reduce labour costs, and mitigate the risk of human error, thereby ensuring seamless scalability and operational efficiency.
Conclusion:
In conclusion, innovations in plastic injection mould toolmaking are catalysing a paradigm shift in the manufacturing landscape, driving significant improvements in efficiency, quality, and cost-effectiveness. From advancements in materials and machining technologies to the proliferation of additive manufacturing and the integration of automation and robotics, these innovations are poised to redefine the boundaries of what is achievable in the realm of injection moulding production. As manufacturers continue to embrace these technologies and methodologies, the future holds promise for a more agile, adaptable, and sustainable manufacturing ecosystem.