Advantages And Challenges of Sponge Extrusion
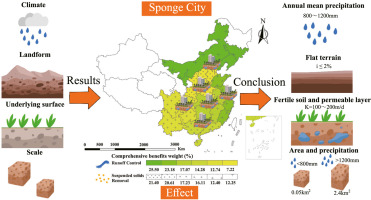
Sponge or expanded foam rubber is resilient and comes in various forms. These sponge extrusions are essential for many industries. This is because they make cellular construction more flexible and compressible. Sponge extrusions are usually made of silicone and synthetic rubber.
In this blog, we will uncover the advantages and disadvantages of sponge extrusions. Stick around and add to your knowledge regarding the sponge extrusions.
How is Sponge Rubber Manufactured?
Let’s dig into how sponge rubber is manufactured while we are at it. You should know that the invention of sponge rubber dates back to the early 20th century. This century, we have an ever-increasing demand for compressible materials. Hence, researchers then invented them.
They added the foaming agent to liquid latex. This produces a cellular structure resembling a sponge. However, with age, chemical engineering and manufacturing have also been refined. This modified manufacturing process results in efficiency. Plus, it enhances the performance of these sponge rubbers.
In the modern era, the manufacturing process includes using additives. These can be curing gents accelerators and mixing them with the raw rubber compounds. After that, the whole mixture is then wiped by hand so that the foaming agent is evenly mixed.
This manufacturing process can vary depending on the sponge rubbers produced. These sponge rubbers are then used to create extruded profiles or even flat sheets. Moreover, the rubber sponge comes in various sizes and lengths. For example, you make a large rectangle from 2 meters wide to 1 meter long. You can also get 6 meters of rubber sponges by connecting multiple sheets of 1-meter length.
Advantages of Sponge Extrusion
Sponge rubber extrusion is a technique for manufacturing rubber strips. Plus, it uses different properties material-wise. There is a list of benefits these sponge extrusions offer you. They can range from compressibility to water and weather resistance.
Here is the breakdown of the advantages of sponge extrusions:
- Compressibility
One forte ofsponge extrusions is that they are flexible enough. Hence, you can compress them based on the available space. They can compress and fill in the random gaps with irregular shapes. The sponge extrusion squashes into the irregular holes and seals the areas. This helps block the influx of water, dirt, or even air.
After the sponge extrusion is removed from compression, it should return to its original shape. In some cases, excessive reduction leads to permanent deformity of the sponge extrusions. You can use a specific technique to avoid such situations.
- Closed-Cell Structure
You can produce the sponge extrusion by the open or closed cell structure. While both types have similar shapes, they still have different properties to offer. These various properties make the sponge extrusions suitable for different industry applications.
The open-cell sponge extrusion is less compression-resistant, softer, and permeable to water. Thus, it can be deployed to absorb and dampen sound waves.
On the other hand, the closed-cell sponge extrusion is impervious to water or air and any other fluid. You can use these sponge extrusions to seal exterior and interior applications. This blocks heat, sound, and moisture from reaching the sealed product.
- Water and Weather Resistance
Depending on the material they are made of, sponge extrusions are usually weather-resistant. For instance, most closed-cell sponge extrusions can also resist water absorption and other fluids.
You can install these sponge extrusions on outdoor applications. This protects your application from elemental factors.
Challenges of Sponge Extrusion
Although sponge extrusions have several benefits, they can still pose particular challenges to users. The most significant one is precision, which is one of the most challenging steps in the manufacturing process.
You must be very careful of parameters during the manufacturing process. It’s essential for producing a perfect sponge extrusion for indoor and outdoor applications. However, this precision is only possible with advanced technology and skilled technicians. When you deploy advanced machinery and skilled labor, your fiscal input touches unrealistic peaks.
In addition, with modern advancement, you can only strive when you take a step further. It might be difficult for manufacturers to produce rubber strips that deploy innovation and promise advancements.
You need suitable testing materials, and your research should be resource-intensive. It’s to be innovative and progressive in sponge extrusion manufacturing. Likewise, when you are producing the sponge extrusion in mass, it might be hard to monitor the quality of the product.
Wrapping Up
Sponge extrusions can have benefits ranging from compressibility to lightweight to weather resistance. However, certain drawbacks can also exist. These can include high costs and increased labor input.
Furthermore, different sponge extrusions can be effective for other sorts of applications. Hence, you should know the best sponge extrusions that fit your requirements.
See also: The Impact of the Paul Mackoul MD Lawsuit Women’s Health Care