Mastering Precision: The Art and Science of Spray Booth Powder Coating
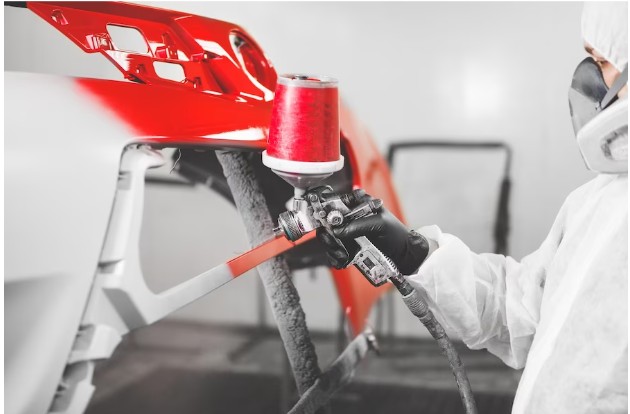
In the realm of industrial finishing, the process of powder coating stands out as a versatile and highly effective method for applying a durable and attractive finish to various surfaces.
When combined with the controlled environment of a spray booth, powder coating reaches new heights of precision and efficiency.
This exploration dives into the intricate world of spray booth powder coating, unraveling the techniques, benefits, and transformative impact this tandem brings to the finishing industry.
Understanding Powder Coating: A Brief Overview
Before delving into the nuances of spray booth powder coating, it’s essential to grasp the fundamentals of powder coating itself.
Powder coating is a dry finishing process where a finely ground, electrostatically charged powder is applied to a surface.
The object to be coated is then cured in an oven, allowing the powder to melt and form a smooth, durable, and uniform coating.
The powder used in this process can be made from a variety of materials, most commonly epoxy, polyester, or a blend of both.
The choice of powder depends on the desired finish properties, such as durability, color retention, and resistance to environmental factors.
The Role of Spray Booths in Powder Coating Precision
Spray booths serve as controlled environments designed to optimize the powder coating process.
These booths provide a clean and controlled space where the application of powder is precise, and environmental factors are minimized, ensuring a high-quality finish. Here’s how spray booths enhance the precision of powder coating:
- Temperature and Humidity Control:
Maintaining consistent temperature and humidity levels is crucial for achieving optimal powder coating results.
Spray booths are equipped with climate control systems that regulate these factors, reducing the risk of defects caused by variations in environmental conditions.
This level of control is particularly important during the curing stage when the coated object is exposed to heat to achieve a durable finish.
- Dust and Contaminant Prevention:
Even the smallest particles of dust or contaminants can compromise the integrity of a powder-coated finish.
Spray booths feature advanced filtration systems that remove airborne particles, ensuring a clean environment for the coating process.
This meticulous attention to cleanliness is essential for achieving a flawless and blemish-free finish.
- Uniform Powder Application:
Achieving a uniform and even application of powder is a cornerstone of successful powder coating.
Spray booths are designed with precision in mind, featuring systems that facilitate consistent powder distribution.
The electrostatic charge applied to the powder ensures that it adheres evenly to the object’s surface, resulting in a smooth and consistent finish.
- Ventilation and Extraction:
Proper ventilation is essential to ensure the safety of operators and the efficient removal of excess powder.
Spray booths are equipped with ventilation systems that extract overspray, directing it away from the coated object and preventing it from settling on surfaces.
This not only enhances the quality of the finish but also contributes to a safer working environment.
- Reduced Contamination Risks:
Spray booths create a confined space where the risk of external contamination is significantly reduced.
By isolating the coating process from external elements, spray booths contribute to the production of high-quality, contaminant-free finishes. This is particularly crucial in industries where precision and consistency are paramount.
Benefits of Spray Booth Powder Coating
The marriage of powder coating and spray booths offers a myriad of benefits across various industries. Here are some key advantages:
- Durability and Longevity:
Powder coating, when applied in a controlled environment, results in a highly durable finish. The cured powder forms a resilient surface that resists chipping, scratching, and fading, ensuring the longevity of the coated object.
This makes spray booth powder coating particularly advantageous for applications where durability is paramount, such as automotive components and outdoor furniture.
- Environmentally Friendly:
Unlike traditional liquid coatings that may contain volatile organic compounds (VOCs), powder coatings are environmentally friendly.
The absence of solvents in powder formulations reduces the release of harmful pollutants. When combined with the efficient extraction and filtration systems of spray booths, the overall environmental impact is minimized.
- Color and Finish Options:
Spray booth powder coating offers a wide range of color and finish options. Whether a glossy, matte, or textured finish is desired, the controlled application process ensures that the coating adheres uniformly, resulting in a consistent appearance.
This versatility makes powder coating suitable for diverse applications, from consumer electronics to architectural elements.
- Cost-Efficiency:
The efficiency of the powder coating process, coupled with reduced material wastage in a controlled spray booth environment, contributes to cost savings.
Powder coating systems are known for their high transfer efficiency, meaning a significant portion of the applied powder adheres to the object, reducing the need for additional coating material.
- Quick Curing Times:
The curing process in powder coating is relatively quick compared to some traditional liquid coatings.
This accelerated curing, facilitated by the controlled conditions of a spray booth, enhances production efficiency, allowing for faster turnaround times and increased throughput.
Applications Across Industries: Where Precision Meets Performance
Spray booth powder coating finds applications across a spectrum of industries, each benefiting from the precision and performance this finishing method delivers:
- Automotive Components:
From alloy wheels to chassis components, automotive manufacturers leverage spray booth powder coating for its durability and resistance to road conditions and weather exposure. The controlled application environment ensures a flawless finish on critical automotive parts.
- Architectural Elements:
Architectural features, such as aluminum extrusions, window frames, and metal facades, benefit from the uniform and lasting finish provided by spray booth powder coating. The ability to choose from a vast color palette and finishes allows architects and designers to achieve their aesthetic vision with precision.
- Consumer Electronics:
The sleek finishes on consumer electronics, from smartphones to gaming consoles, are often the result of powder coating in a controlled spray booth environment.
The uniform application of powder ensures a visually appealing and scratch-resistant surface on electronic devices.
- Furniture and Outdoor Equipment:
Powder coating plays a vital role in enhancing the aesthetics and durability of furniture, outdoor equipment, and recreational items.
Patio furniture, playground equipment, and garden tools benefit from the protective and weather-resistant properties of powder-coated finishes.
- Industrial Machinery:
Manufacturers of industrial machinery and equipment rely on spray booth powder coating for its ability to withstand harsh operating conditions.
The even application of powder in a controlled environment ensures that critical machinery components are well-protected against wear and corrosion.
Challenges and Considerations in Spray Booth Powder Coating
While spray booth powder coating offers numerous advantages, there are considerations and challenges to bear in mind:
- Equipment Investment:
Setting up a spray booth with the necessary climate control and filtration systems involves an initial investment.
However, this investment pays off in the form of consistent, high-quality finishes and long-term cost savings.
- Space Requirements:
Spray booths require space for installation and operation. The available space should accommodate the booth itself, as well as the necessary safety measures and ventilation systems.
This consideration is especially relevant for smaller facilities or businesses with limited floor space.
- Operator Training:
Proper training is essential for operators working with spray booth powder coating systems. Understanding the nuances of the process, from powder application to curing, ensures that the coating is applied accurately and efficiently. Operator training also contributes to workplace safety.
- Maintenance and Cleaning:
Regular maintenance of spray booths is essential to ensure optimal performance. This includes cleaning filters, checking ventilation systems, and monitoring equipment for wear and tear.
Routine maintenance not only prolongs the life of the spray booth but also contributes to the consistency of the coating process.
The Future of Spray Booth Powder Coating: Advancements and Innovations
As technology continues to advance, the world of spray booth powder coating evolves with new innovations and capabilities. Some key trends and advancements shaping the future of this industry include:
- Smart Coating Technologies:
The integration of smart technologies into powder coating equipment and spray booths enhances precision and efficiency.
Automated systems with sensors and feedback mechanisms enable real-time monitoring, ensuring optimal coating results.
- Digitalization and Color Matching:
Digital color matching technologies are becoming more prevalent, allowing for precise color reproduction in powder coatings.
This digitalization streamlines the process of selecting and achieving specific color finishes, catering to the diverse aesthetic preferences of industries such as automotive and consumer goods.
- Energy-Efficient Solutions:
Advancements in energy-efficient technologies contribute to sustainable powder coating practices.
Spray booths equipped with energy-efficient curing systems and climate control measures reduce energy consumption, aligning with the growing emphasis on environmental responsibility.
- Customization and On-Demand Coating:
The ability to offer on-demand coating solutions and customization continues to gain importance.
Spray booths equipped with adaptable systems allow manufacturers to quickly switch between different coating formulations and finishes, meeting the demand for personalized products.
Conclusion: Precision, Efficiency, and Enduring Finishes
Spray booth powder coating epitomizes the synergy between precision and efficiency in the world of industrial finishing.
From automotive components to architectural elements and consumer electronics, the transformative power of this coating method is evident in the enduring finishes it delivers.
As industries evolve and consumer expectations rise, the role of spray booth powder coating remains pivotal in meeting the demand for high-quality, visually appealing, and long-lasting coated products.
In the journey toward precision and enduring finishes, the marriage of powder coating and spray booths stands as a testament to the industry’s commitment to excellence.
As technology continues to propel this field forward, the future promises innovations that will further refine the art and science of spray booth powder coating, ensuring that each coated surface is a masterpiece of durability, aesthetics, and lasting performance.