Turbocharged Recovery: Next-Gen Solutions for Gas Turbine Maintenance
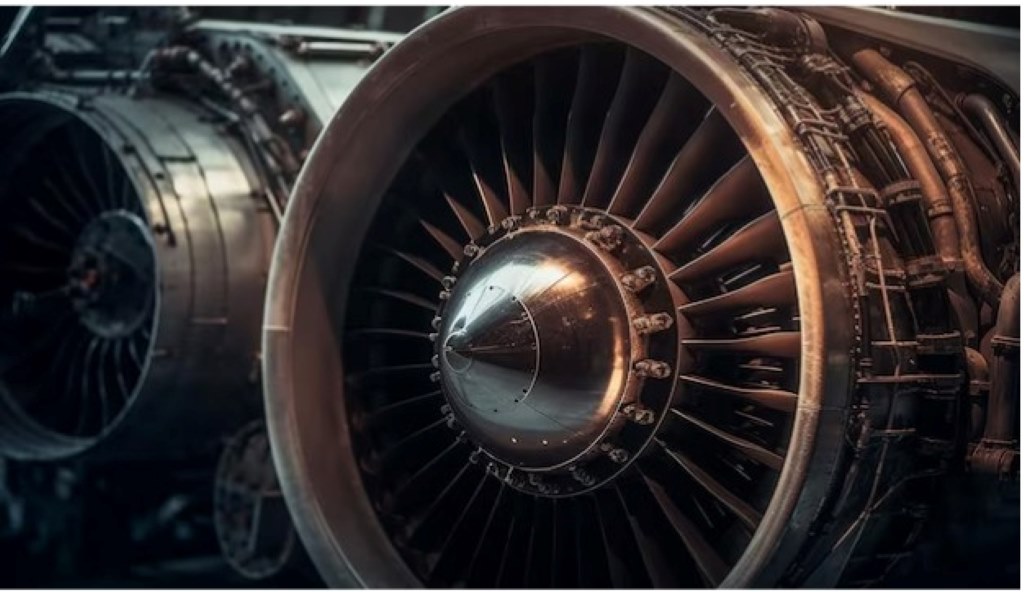
In the field of energy production gas turbines play a role in powering industries such as power plants and aviation. To ensure these turbines continue to operate and reliably it has become essential to explore maintenance solutions. This article delves into the cutting edge solutions that are revolutionizing the recovery and maintenance of gas turbines.
1. Anticipatory Maintenance Systems
The emergence of maintenance systems represents a shift in gas turbine maintenance practices. Traditional schedules based on hours are now being replaced by algorithms and sensor technologies. Anticipatory maintenance utilizes real time data analysis to predict issues before they escalate into problems. By monitoring parameters like vibration, temperature and pressure these systems can accurately estimate the remaining lifespan of turbine components and schedule maintenance activities when necessary. This approach not minimizes downtime but also extends the longevity of gas turbines.
2. Enhanced Monitoring and Diagnostic Capabilities
Next generation gas turbine maintenance relies on monitoring and diagnostic tools that provide insights, into turbine performance. Remote monitoring systems equipped with sensors and IoT technologies enable surveillance of parameters.
In the event that there are any deviations, from the operating conditions these systems will generate alerts enabling maintenance teams to take action. Additionally advanced diagnostic tools utilize data analytics and machine learning to identify patterns and anomalies which helps in detecting issues at a stage.
3. Utilizing 3D Printing for Replacing Components
The innovation of manufacturing, commonly known as printing has completely transformed the production of replacement parts for gas turbines. Traditional methods often involve procurement processes and come with costs; however with 3D printing complex components can be rapidly fabricated with precision. This not speeds up the maintenance process. Also provides the flexibility to create customized parts that deliver high performance. Moreover utilizing materials, in 3D printing further enhances the durability and efficiency of these components.
4. Robotics and Drone Application in Inspection
Gas turbines are systems with components located in to reach areas. Traditional inspection methods involve time consuming and sometimes risky processes. However the integration of robotics and drones is revolutionizing the maintenance of gas turbines. Drones equipped with cameras and sensors can navigate through turbine structures capturing detailed images for inspection purposes. At the time robotic systems that are specifically designed to withstand environments can carry out tasks like cleaning, repairs and even component replacements with utmost precision.
5. Augmented Reality (AR) for Training and Maintenance
The utilization of reality has significantly improved training and maintenance procedures for gas turbines. Maintenance technicians can now wear AR enabled devices that overlay information onto the physical turbine components. This immersive technology provides step by step guidance for maintenance tasks reducing the chances of errors and enhancing efficiency. Additionally AR is being used to provide assistance where experts can guide on site technicians in time regardless of their geographical location.
6. Condition Based Overhaul
Continuous monitoring and analyzing the data help identify when components are nearing the end of their life cycle prompting overhauls. This method aims to minimize any downtime and lower maintenance costs. By prioritizing the components that need attention condition based overhaul strategies ensure allocation of resources and contribute to the long term well being of gas turbines.
7. Sustainable Practices for Gas Turbine Maintenance
As the world moves towards a future the field of gas turbine maintenance is also embracing eco friendly practices. The use of lubricants, friendly cleaning methods and the recycling of turbine components are becoming essential components of modern maintenance strategies. These practices not align with social responsibility goals but also contribute to the overall sustainability of the energy industry.
In conclusion
Gas turbine maintenance is undergoing a shift driven by advancements and a commitment to efficiency and sustainability. Predictive maintenance, advanced monitoring techniques, 3D printing, robotics, augmented reality applications, condition based overhauls and sustainable practices are among the elements propelling gas turbine recovery into an era.
By adopting these next generation solutions industries reliant on gas turbines can significantly reduce downtime improve efficiency levels and extend the lifespan of their assets. As we continue to unlock the potential of technology, in this field the recovery and optimization of gas turbines become not necessary. Also lead us towards a future where cleaner and more reliable energy production is achieved.